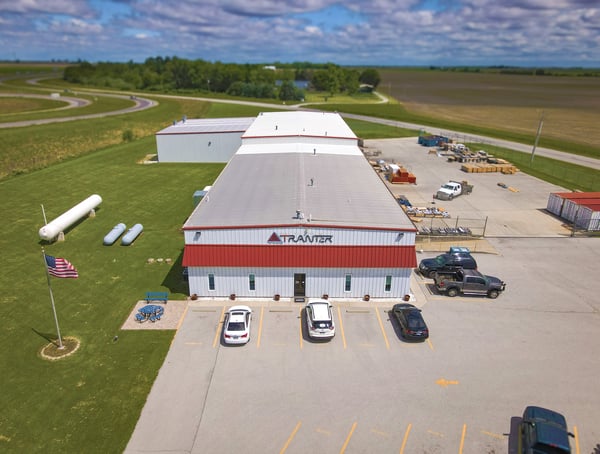
Resource center
Articles
There's more
Videos and explainer series
Parts and services
When it comes to inspection and plate removal, it's crucial to pay attention to every detail. By following the necessary steps and taking the time to inspect and remove plates properly, we can ensure that your project is completed successfully. Learn more by listening to Dave Lusignolo, Director, Aftermarket Sales - North America
Parts and services
Chemical cleaning and rinse are essential steps in maintaining the performance of your heat exchanger. Whether it's removing liquids, or ensuring the longevity of machinery, chemical cleaning and rinse play a crucial role in the service process.
Guides and literature
Energy, heating and cooling Sustainability
The digitalization mega trend has resulted in exponential growth of data centers. Let’s take a look at how Tranter’s plate and frame heat exchangers can be used to make the datacenters more sustainable.
Energy, Process industries Sustainability
Tranter’s heat exchangers have various applications across many different markets. Let’s take a look at how plate and frame heat exchangers can be used in CO2 capture applications to improve the total economy of the plant.
Energy, Process industries
Tranter’s compact plate heat exchangers are used in various energy intense industrial applications. Let’s take a look at how plate heat exchangers can be used in the production of green hydrogen and in the hydrogen value chain.
Sustainability Energy, heating and cooling Energy, Process industries
Explore our comprehensive brochure to delve deeper into Tranter and discover the wide range of offerings we provide.
Parts and services
With regular service and maintenance you will keep control of your heat exchangers conditions and maintain optimal performance. Learn more from this simplified quick guide.
Energy, heating and cooling Energy, Process industries Marine and shipbuilding
For increased durability and energy efficiency. Get some more insights to our welded block heat exchanger with this guide.
Energy, heating and cooling Energy, Process industries Marine and shipbuilding
Now you can obtain the thermal efficiency and compactness of gasketed heat exchangers in elevated pressure/high-and-low temperature applications. Learn more about our shell and plate heat exchanger.
Energy, heating and cooling Energy, Process industries Sustainability
Optimum performance is a promise Tranter has been fulfilling for many decades with the Superchanger® plate and frame heat exchanger.
Energy, heating and cooling
Selecting a heat exchanger is not just about finding an option that fits within your budget. Your choice should strike an optimal balance between cost and performance. Otherwise, you could end up with a unit that’s not designed for its purpose. This mistake can be costly. So, how do you know which exchanger is right for you?
Parts and services
Are you tired of feeling like your heat exchanger is draining your wallet like a car engine left running all night? Our guide walks you through the steps you need to take – from pre-purchase and design to maintenance – to get the most out of your heat exchanger.
Energy, Process industries Sustainability Parts and services
Each process is unique, demanding a specific type of heat exchanger to match. This comprehensive guide and checklist, drawn from 90+ years of experience, will help you select a heat exchanger that fits and enhances the efficiency and effectiveness of your process.
Marine and shipbuilding
As a Vessel Manager, you know how much rides on choosing the right heat exchanger service provider. This guide breaks down the critical factors to consider—preparation, expertise, global reach, and more—so you can make informed decisions and avoid downtime, delays, or unexpected costs.
educational webinars