Case study: Exchanging waste for money

How to turn flue gas into valuable heat recovery
The opportunity
At SYSAV’s waste-to-energy plant in Malmö, Sweden, they found a way to do just that — with the help of Tranter’s plate and frame heat exchangers (PHEs). By capturing heat from boiler flue gas condensate, SYSAV is now reclaiming energy that would have gone to waste, directly feeding it back into the district heating loop.
The result?
- A 20% increase in thermal efficiency
- Significant energy savings
- No increase in emissions
The mission
SYSAV’s core mission is environmentally responsible waste management and energy recovery. But tightening EU emissions standards meant they needed to level up their operations. As part of a 200 million SEK (~$26 million USD) upgrade, SYSAV installed a modern, four-stage wet flue gas scrubbing and heat recovery system across two boiler lines — alongside a broader upgrade of their waste-fired boilers.
This plant is no small operation:
- Three waste-fired boilers feeding the Malmö and Burlöv district heating network
- One boiler alone produces ~145,000 MWh/year of electricity
- The energy delivered covers 40% of the district heating demand — set to reach 50% as expansions continue
- That’s enough to heat 80,000 apartments annually, equivalent to the energy in 100,000 tons of heating oil
But the flue gas cleaning process was leaving valuable energy on the table. SYSAV saw an opportunity to capture it — and that’s where Tranter came in.
The solution
When flue gases are scrubbed with water cooler than the gas’ dew point, condensation occurs. SYSAV capitalized on this by installing Tranter’s GXD-205 plate and frame heat exchanger to capture that heat efficiently.
Here’s how the system works:
- Hot condensate from the top stage of the scrubber is passed through the GXD-205, which transfers heat to the district heating loop.
- An in-line strainer at the condensate inlet captures particulates from the flue gas.
- The condensate is cooled to just 1–2°C above the district heating water’s inlet temperature, maximizing energy transfer.
- Additional units complete the cooling process:
- A Tranter GCD-016 PHE uses district heating water to cool condensate from Stage 4.
- A Tranter GLD-013 PHE uses groundwater to further cool Stage 4 water and process water from Stage 3 (the sulfur dioxide step).
- All three units are built with 254 SMO™ stainless steel (1.4547) to handle the aggressive chlorides and fluorides present in the flue gas condensate.
Why Tranter?
The project engineers at Götaverken Miljö chose Tranter’s PHEs over traditional shell-and-tube heat exchangers for several key reasons:
- Superior cost-efficiency, especially with high material costs
- Compact footprint, reducing installation complexity
- Proven technical support and solution design
For you, these are the wins that matter: equipment that’s engineered for fast installs, smart space usage, and durability in harsh conditions — all delivered by a partner who knows the job isn’t done until it’s working perfectly on-site.
The impact
SYSAV’s heat recovery strategy doesn’t just work on paper — it’s delivering real, measurable gains. By capturing waste heat from flue gas streams above 150°C (300°F), SYSAV significantly improved its thermal efficiency with no added emissions.
For similar heating and cooling projects, this strategy has broad application potential:
- Heat recovery from any boiler flue gas stream above 150°C
- Even greater efficiency gains when paired with heat pumps
- Significant fuel savings and shorter payback periods
When you’re juggling tight deadlines, complex installations, and cost control, these aren’t nice-to-haves — they’re the difference between a good project and a great one.
Want to unlock hidden energy savings in your next project?
Let’s talk about how Tranter’s heat exchangers can turn waste into value.
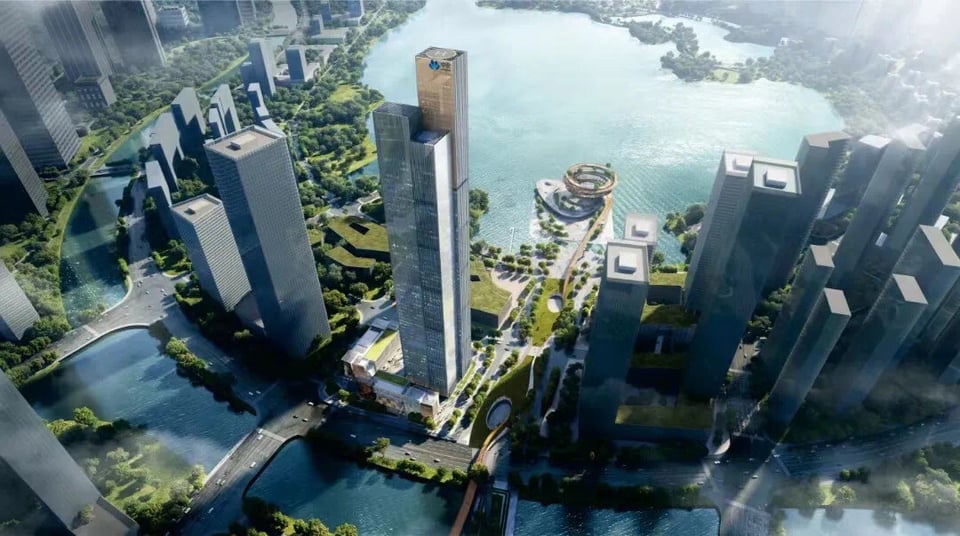
latest customer case
Tranter China joins hands with Jinmao to create a new model of sustainability
Energy, Heating and cooling