Energy, Process industries Parts and services
Why customized maintenance is your best choice for heat exchanger health
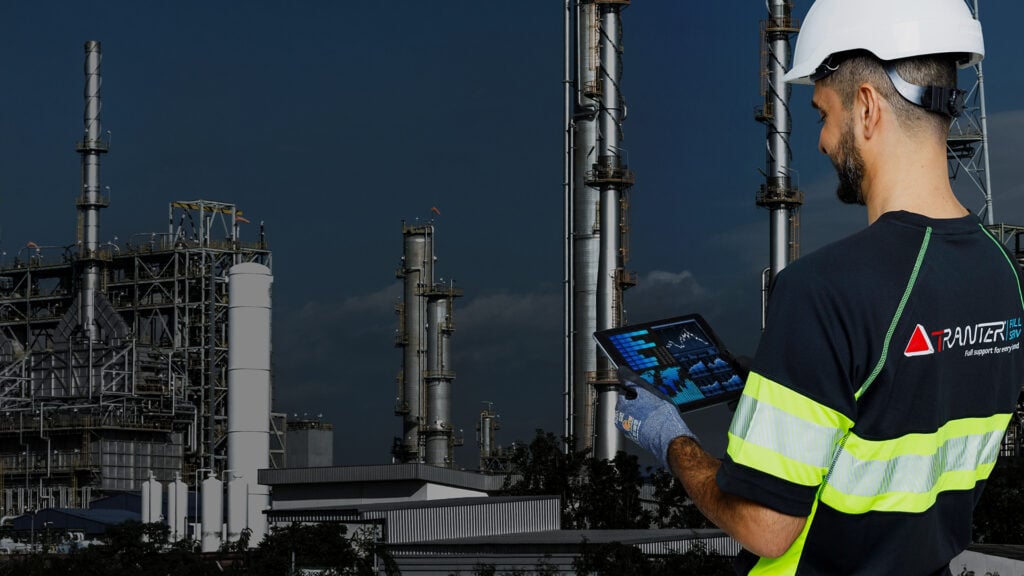
Plant Engineers often grapple with a multitude of questions surrounding heat exchanger maintenance. But what if you had a tailored solution designed specifically for your plant’s unique challenges and requirements? Dive into Tranter’s customized maintenance, where every twist and turn is anticipated, ensuring your exchanger’s longevity and peak performance.
Service contracts that streamline maintenance (and reduce costs)
Many service providers offer seemingly similar packages. However, they often come with unexpected costs, fluctuating service rates, inconsistent maintenance schedules, and the hassles of constantly renegotiating terms. As a result, your need for a dependable, cost-effective, and streamlined maintenance solution becomes paramount.
Tranter’s commitment is for you to sidestep these challenges. At the heart of our service model lies our distinctive service contract approach, which includes:
- Customized contracts: Every heat exchanger has its unique needs. Our contracts are specifically tailored to ensure timely and appropriate service for each unit.
- Cost efficiency: Efficient maintenance means cost savings. By streamlining our service contracts, we avoid unnecessary interventions, saving you both time and money.
- Fixed and reduced pricing: Our contracts come with reduced rates (in contrast to ad-hoc maintenance), cementing our commitment to long-term relationships. And guess what? The rates remain the same throughout the contract, shielding you from unpredictable market changes.
- Readiness and convenience: Our service contract means we’re always ready, with parts and services aligned to your maintenance schedule. No surprises, just timely execution.
- Peace of mind: We handle the complex details of your maintenance plan, so you don’t have to.
The key to constant efficiency: Proactivity
How well do your heat exchangers stand the test of time? Just like any hardworking machine, they’re not impervious to wear and tear. Over time, degradation challenges arise, leading to diminished heat transfer capabilities. In contexts like ethanol production, where precision is paramount, insufficient heat transfer can be the difference between hitting the mark and missing it. And missing it is costly, not only in terms of production but also in operational costs.
But here’s the real question: Why wait for lost production when you can prevent it?
At Tranter, we don’t offer just another maintenance plan. No, ours is a strategy tailored to your heat exchanger’s unique operational demands. We don’t just respond to degradation; we anticipate and manage it. The result? Your heat exchangers consistently operate at peak performance. This proactive approach not only safeguards your processes but also translates to tangible savings in operational costs.
Parts will always be accessible (even those special ones)
Imagine being in the middle of an important process in your plant and having a vital component of your heat exchanger break down. The immediate reaction? Panic. Especially if there’s no replacement part at hand. That’s the harsh reality of the ‘run-to-failure’ approach. Sure, it might seem like a money-saver initially, but the risks and surprise costs can easily overshadow those savings.
We decided there was a better way. Knowing that even a minor component’s unavailability can lead to prolonged downtimes, our solution revolves around being prepared. With a robust inventory management system, we’ve ensured that we’re not just stocked up but stocked right. From generic to specialized components, if your heat exchanger needs it, we have it. So whether you’re planning routine maintenance or facing an unexpected hiccup, we’ve got your back.
Different heat exchangers require different treatment
Ever tried juggling? Now, imagine each ball representing a different heat exchanger in your plant. Drop one, and the entire act falls apart. Plant Engineers like yourself understand this all too well. Each heat exchanger has its own quirks and needs, making a one-size-fits-all maintenance approach a recipe for disaster.
At Tranter, we don’t believe in generic solutions. Instead, we dive deep into understanding the distinct nature of each heat exchanger you manage. From cataloging every exchanger to tuning into your plant’s unique operational rhythms, we ensure the maintenance plan we create for you are as unique as the heat exchangers they serve. Whether it’s about managing the intricacies of a two-week shutdown or catering to specific service demands, we craft your maintenance calendars with precision.
PRO INSIGHT:
Tranter’s approach is as collaborative as it is technical. We actively engage with you to understand your overarching unique challenges and aspirations. This ensures that the maintenance roadmap we design not only prioritizes the health and efficiency of your heat exchangers but also aligns seamlessly with the broader operational goals and realities of your facility.
How do you finish a puzzle without a reference picture?
Imagine being handed a jigsaw puzzle with a thousand pieces – but without a reference picture. Each piece represents a brand, model, or aspect of your heat exchangers, and as a Plant Engineer, you’re tasked with fitting them all together seamlessly. The challenge? Deciphering how each piece relates to the others, anticipating potential maintenance pitfalls, and ensuring the entire system operates smoothly. It’s a daunting task that requires expertise, foresight, and intricate knowledge of every tiny detail.
Enter Tranter: Your puzzle reference picture. With knowledge cultivated over 90+ years, we clarify the complex jigsaw of heat exchangers. Being an OEM, we’re not just familiar with each piece; we understand how they interconnect, the intricacies of their designs, and the reasons behind their specific operational requirements. Our expertise means you don’t just assemble the puzzle blindly; you do so with a clear vision and purpose.
PRO INSIGHT:
Apart from assisting with assembling the puzzle, we also anticipate where potential challenges might emerge and address them proactively. Missing or misplacing even one puzzle piece can disrupt your entire system. With our guidance, every piece will fit exactly where it should, ensuring your heat exchangers function optimally and consistently.
What it’s all about
Plant Engineers often grapple with a critical dilemma: How to strike the right balance between budget constraints and the undeniable importance of effective maintenance. Can you cut corners without jeopardizing equipment performance and longevity? And without proactive oversight, how do you anticipate and mitigate those unexpected yet inevitable hiccups?
The answer isn’t in mere cost-savings but in smart resource allocation. By investing in proactive oversight and tailored maintenance strategies, you not only safeguard equipment performance but also preempt and counter those unforeseen challenges that can disrupt operations. The key is not to spend less but to spend wisely, ensuring every dollar goes to longevity and efficiency.
That’s why Tranter’s approach goes beyond traditional service models. We specialize in offering customized maintenance solutions that align with your budget while ensuring no compromise on equipment health. By harnessing our in-depth expertise and industry insights, we provide proactive strategies that anticipate challenges before they escalate.
Keen to know more about our customized maintenance solutions? Have a chat with one of our experts and find out how we can create the optimal plan for you and your plant.