Full service support for every brand
Regardless of the brand of your plate heat exchangers, Tranter's expert service teams are on standby to restore your systems to peak efficiency, anywhere in the world your facility may be located.
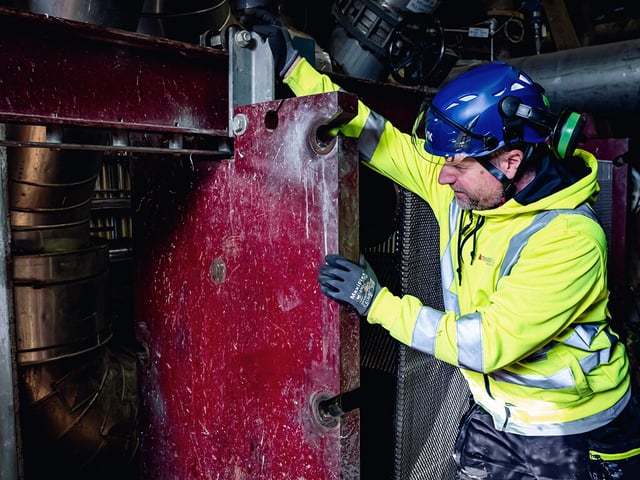
- Efficient and reliable heat transfer for every industry
- The best choice for challenging applications.
- For increased durability and energy efficiency.
BRINGING EFFICIENCY TO HEAT TRANSFER
Regardless of the brand of your plate heat exchangers, Tranter's expert service teams are on standby to restore your systems to peak efficiency, anywhere in the world your facility may be located.
Experience performance at its peak - that's the promise of Tranter, backed by our specialized knowledge in providing heat transfer solutions for every industry.
Tranter proudly holds ISO certification, demonstrating our unwavering commitment to excellence in both design and manufacturing processes.
INNOVATION AND PRODUCT DEVELOPMENT
resource center
Energy, heating and cooling Sustainability
The digitalization mega trend has resulted in exponential growth of data centers. Let’s take a look at how Tranter’s plate and frame heat exchangers can be used to make the datacenters more sustainable.
Energy, Process industries Sustainability
Tranter’s heat exchangers have various applications across many different markets. Let’s take a look at how plate and frame heat exchangers can be used in CO2 capture applications to improve the total economy of the plant.
Energy, Process industries
Tranter’s compact plate heat exchangers are used in various energy intense industrial applications. Let’s take a look at how plate heat exchangers can be used in the production of green hydrogen and in the hydrogen value chain.
Are you considering acquiring heat exchangers?